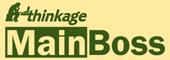 |
Planned Maintenance
|
This help file applies to an out-of-date version of MainBoss.
The most recent version of MainBoss is MainBoss 4.2.4.
For the latest version of this help file can be found here.
< Previous section | Table of Contents | Index | Next section >
Scheduling Planned Maintenance gives a step-by-step overview of how to schedule planned maintenance operations. It shows the typical pattern of how you use MainBoss to create a task description, how you assign units to that task, and how you use MainBoss to generate planned work orders automatically. You will find it useful to read the overview before reading the details contained in this chapter.
As a quick review, here are the elements of MainBoss's planned maintenance facilities:
- Tasks: A task record describes what should be done in a planned maintenance job. It might provide step-by-step instructions or a checklist of actions to take. For example, a task record might describe what should be done in a car oil change. For more, see Tasks.
- Maintenance Timing: A maintenance timing record tells when a job should be done, either in terms of the calendar (e.g. "every three months") or in terms of a meter (e.g. "every 3000 miles"). For more, see Maintenance Timings.
- Unit Maintenance Plans: A unit maintenance plan combines a task, a maintenance timing record, and a unit. For example, the task might be an oil change, the timing might be "every 3000 miles" and the unit might be a particular car; the unit maintenance plan indicates that the car needs an oil change every 3000 miles. Note that you can specify the same task and timing record for a lot of different units; for example, you might specify an oil change every 3000 miles for each car you maintain. For more about unit maintenance plans, see Unit Maintenance Plans.
- Generating Work Orders: On a regular schedule (e.g. once a week), you ask MainBoss to create new planned maintenance work orders. You do this through Unit Maintenance Plans | Generate Planned Maintenance in the control panel, which gives you the planned maintenance generation table viewer. This table contains a record for each previous time you generated planned maintenance work orders. Each record lists the time that you generated the work orders and lists the work orders that were created. This means that you have a history of all the PM work orders you've previously created. For more about the planned maintenance generation table viewer, see Viewing Planned Maintenance Generation Records.
Important: MainBoss does not generate planned maintenance work orders until you tell it to do so! For example, you might tell MainBoss to generate planned maintenance work orders for the next week; MainBoss will then figure out what jobs need to be done in that week and will generate the necessary work orders. However, the work orders are not created until you explicitly tell MainBoss to generate them.
PM Work Orders: You create planned maintenance work orders like this:
- In the control panel, go to Unit Maintenance Plans | Generate Planned Maintenance.
- Click New Planned Maintenance Batch to begin generating new work orders. This opens a window for the generation process.
- In "End Date" fill in a date up to which work orders should be generated. For example, if you want to deal with all planned maintenance that should be done by next Monday, put in next Monday's date.
- In "Maintenance Plans" select the set of unit maintenance plans for which you wish to generate work orders. By default, all plans are selected; however, you can choose a subset of the plans if you wish.
- Click Generate. The Generation Details section will display any work that ought to be done in the given period.
- Examine the information in the Generation Details section. By clicking on a line, you can see information such as the unit, the date on which the PM job should start, and other useful data.
- At this point, the work orders haven't actually been created—MainBoss has only determined which work orders should be created if you choose to go ahead. If you see any surprises in the list, you still have a chance to make corrections. This is particularly useful when you're first setting up your PM schedules—you can set up a schedule, test how it works, and correct any problems...all without actually creating any real work orders.
If you decide something needs to be corrected (for example, a timing record needs to be fixed), click Change Scheduling Parameters. This clears the Generation Details section; you can then change maintenance timing record or anything else related to planned maintenance. Click Generate again to regenerate a new list of tentative planned maintenance jobs.
- When you're satisfied with the Generation Details list, click Commit to create the actual work orders. The creation process may take a considerable amount of time, especially if there are a lot of work orders to make.
Generation Interval: Planned maintenance works best if you generate PM work orders on a regular basis. For example, each Friday, you might generate work orders for the following week (from Monday to Sunday). By generating the work orders ahead of time, you have advance warning of what work you'll have to do. You can even generate work orders farther in advance; each Monday, you might generate work orders for the week beginning the following Monday, giving every a week's notice of what PM jobs are necessary.
To make it easier for you to generate PM work orders on a regular basis, MainBoss lets you set a value called the "Generation Interval". This indicates how often you intend to generate new PM work orders. The time is measured in days; for example, if you set "Generation Interval" to 7, it means you intend to generate PM work orders once a week. If you set "Generation Interval" to 14, it means you intend to generate PM work orders every two weeks.
MainBoss uses your "Generation Interval" value when setting a default for "End Date". The new end date will be calculated by adding "Generation Interval" to the previous end date—the last time you generated PM work orders. For example, suppose "Generation Interval" is 7 and the last time you generated work orders, you did so up to January 1. Then the next time you generate work orders, the default will be to generate them up to January 8. The time after that, the default will be to generate them up to January 15, and so on.
You can always change "End Date" from its default value to something else. For example, before you go on vacation, you might generate two or three weeks of work orders rather than only one. Setting "Generation Interval" simply tells MainBoss how to set the end date automatically rather than requiring you to set it by hand.
You set "Generation Interval" like this:
- Select Unit Maintenance Plans | Generate Planned Maintenance from the control panel.
- In the Defaults for Planned Maintenance Batches section, click Edit Defaults.
- MainBoss opens a window where you can set "Generation Interval".
- Once you've set "Generation Interval" to your preferred value, click Save & Close.
- When you return to the previous window, you may have to click
in order to see the value you just set.
Corrective vs. Preventive Maintenance in Reports: Several reports let you distinguish information on preventive (planned) maintenance work orders from information on corrective work orders. This is done using the Is Preventive option in report printing windows.
- If you select Is Preventive under Group by in the Grouping section of a report window, MainBoss groups preventive work orders in one part of the report and all other work orders (i.e. corrective ones) in the other part of the report.
- If you select Is Preventive in the Filters section of a report window, you can specify that you only want to see information on preventive work orders (Is Preventive is True) or only on corrective work orders (Is Preventive is False).
A work order is preventive if it was created by Unit Maintenance Plans | Generate Planned Maintenance. A work order is corrective if it was generated in some other way.
See Also:
< Previous section | Table of Contents | Index | Next section >