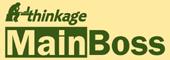 |
The Life Cycle of a Corrective Work Order
|
< Previous section | Table of Contents | Index | Next section >
This section outlines the usual sequence of events in dealing with a problem report received from outside the maintenance department.
- Create a request (see Requests). This is done by the person who receives the problem report.
In some companies, individuals outside the maintenance department may be authorized to prepare their own requests. For example, there might be someone in each department who is authorized to create and submit requests for the maintenance department to deal with.
Requests may also be submitted by email if your site has the MainBoss Service module or through a web page if your site has the Web Requests module.
- Create a work order based on the request (see Work Orders). This is usually done by a maintenance manager. The original request contains a basic description of the problem. The person drawing up the work order may add more information including:
- priority of the job
- date/time the job should be done
- personnel assigned to do the job (possibly including labor costs based on the workers' wages)
- length of time the job is expected to take
- materials expected to be needed for the job
- detailed description of the work to be performed
- You may use assignments to bring the job to the attention of personnel who may have an interest in it. MainBoss automatically creates assignments for people who'll be working on the job, but you may want to create additional assignments for supervisors, clients, and others. For more information, see Assignments.
- Print off the work order and give it to the workers assigned to the job (see Printing Work Orders).
- If your site has the Web Access module, workers can also obtain their work orders by accessing a web page through any web-enabled mobile device, e.g. an iPhone or Android device. Workers may also use work order notes to record comments about a job and to communicate with other MainBoss users. (Notes are more useful than other forms of communication because MainBoss keeps them directly associated with the work order itself. If you use normal email to communicate, there's no connection between the email messages and the work order—the messages will probably get lost. However, if you use MainBoss notes, your database keeps a permanent record of the communications, so information is never lost.)
- During the course of a job, problems may arise that put the job on hold; for example, you may have to wait to get a building permit or customer approval. If so, you can indicate the nature of the hold using status codes. For more information, see Work Order Status Codes.
- Close the work order and the request when the work is actually completed. This may be done by a maintenance manager or by the workers who actually did the job. When you close a work order, you record actual information about the job, as opposed to the estimates you made when you originally created the work order. For example, when you first create a work order, you can estimate the time required for the job and the materials that will probably be used; when you close the work order, you can record the actual time and materials.
You also assign a closing code to each work order. For example, your closing codes may be based on the type of problem (HVAC complaint, plumbing problem, vandalism, etc.) or they might be based on what you did to deal with the problem (repair, replacement, adjustment, etc.). Closing codes provide a way to classify and track the type of work that your maintenance department does.
At any point in the process, you can edit the results of previous stages. For example, when you originally create a work order, you may not have enough information to estimate the expected labor and material costs. When you do get this information, you can go back and add it to the work order.
< Previous section | Table of Contents | Index | Next section >